Landmark Approval
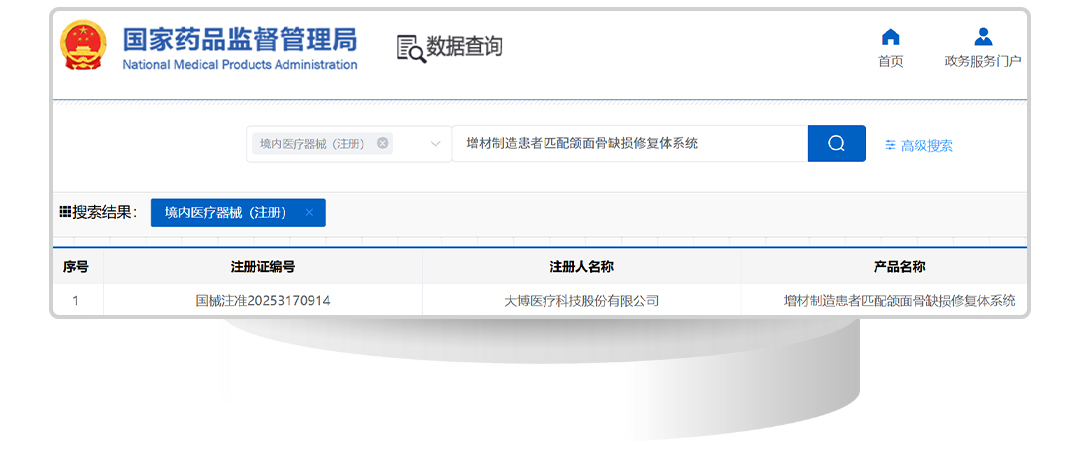
On April 30, 2025, Double Medical's innovative product - the Additively Manufactured Patient-Specific Maxillofacial Bone Defect Reconstruction System - successfully obtained the Class III Medical Device Registration Certificate issued by China's National Medical Products Administration (NMPA). As the highest risk classification in China's medical device regulatory system, Class III certification indicates the product has met rigorous standards for both safety and efficacy, qualifying it for clinical application.
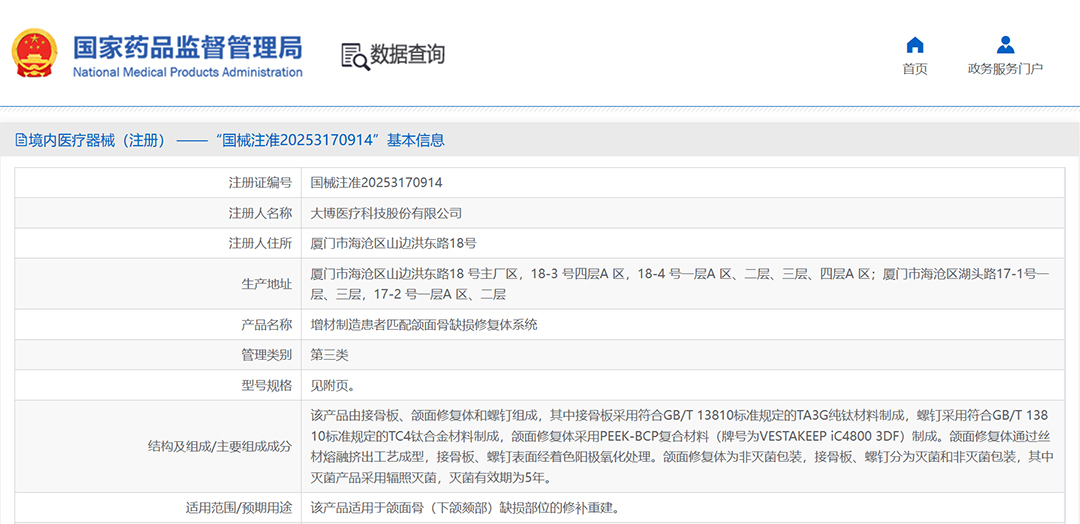
The system is indicated for the reconstruction of maxillofacial bone defects (mandibular chin region), consisting of:
Bone plate: Manufactured from TA3G pure titanium material compliant with GB/T 13810 standards
Screws: Manufactured from TC4 titanium alloy compliant with GB/T 13810 standards
Maxillofacial implant: Made from PEEK-BCP composite material (grade VESTAKEEP® iC4800 3DF). The implant is formed through fused filament fabrication (FFF) process
The bone plates and screws feature colored anodized surface treatment. The maxillofacial implants are provided in non-sterile packaging, while bone plates and screws are available in both sterile and non-sterile packaging. Sterile products undergo radiation sterilization with a 5-year shelf life.
Technical Breakthrough
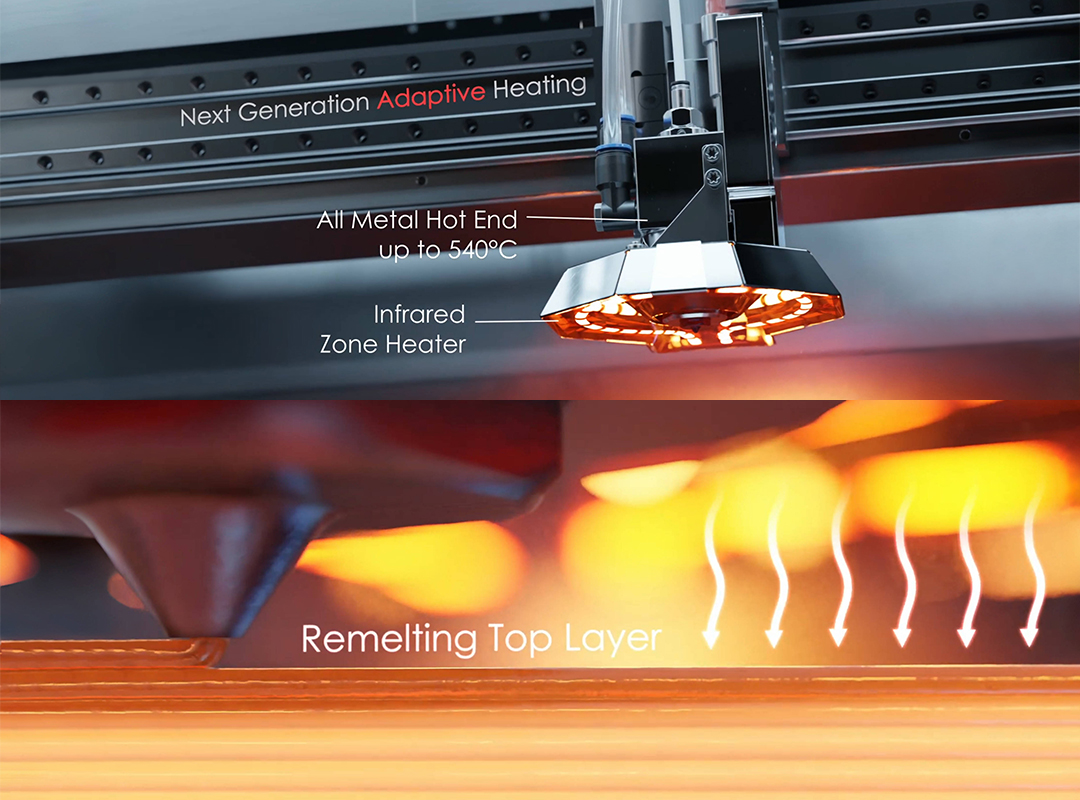
In developing the maxillofacial implant, Double Medical utilized APIUM 3D printers and Evonik's implant-grade PEEK filament, achieving high-precision, customized implant manufacturing through Fused Filament Fabrication (FFF) technology.
This approval not only represents a significant breakthrough for Double Medical in the field of high-end implantable devices, but also demonstrates the vast potential of 3D printing technology in medical applications.
FFF 3D printing technology provides greater design freedom, allowing product developers to focus entirely on patient needs without the constraints of traditional manufacturing methods. This facilitates truly customized treatments that closely match individual patient requirements. Additionally, 3D printing can significantly reduce implant manufacturing lead times while offering greater flexibility to quickly adapt to changing requirements.
Conclusion
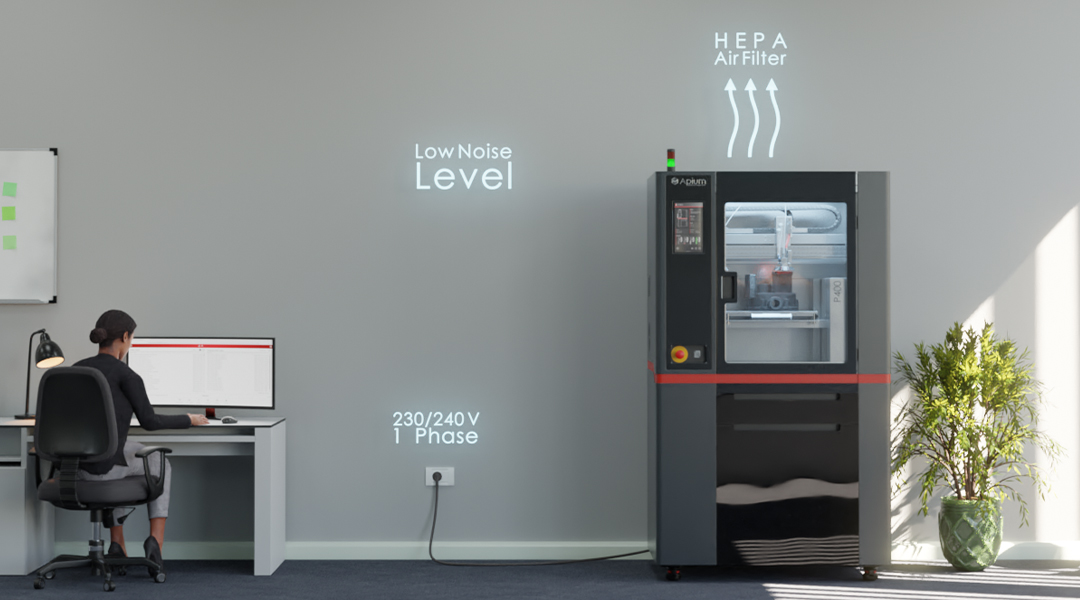
Double Medical's newly approved additively manufactured maxillofacial reconstruction system represents the deep integration of 3D printing technology, advanced biomaterials and clinical medicine. As technology continues to advance, personalized and precise medical solutions will become mainstream in the industry, benefiting more patients.
Gyrotec will continue to advance innovative applications of 3D printing technology in healthcare, working with partners to promote breakthroughs and development in China's high-end medical device sector!
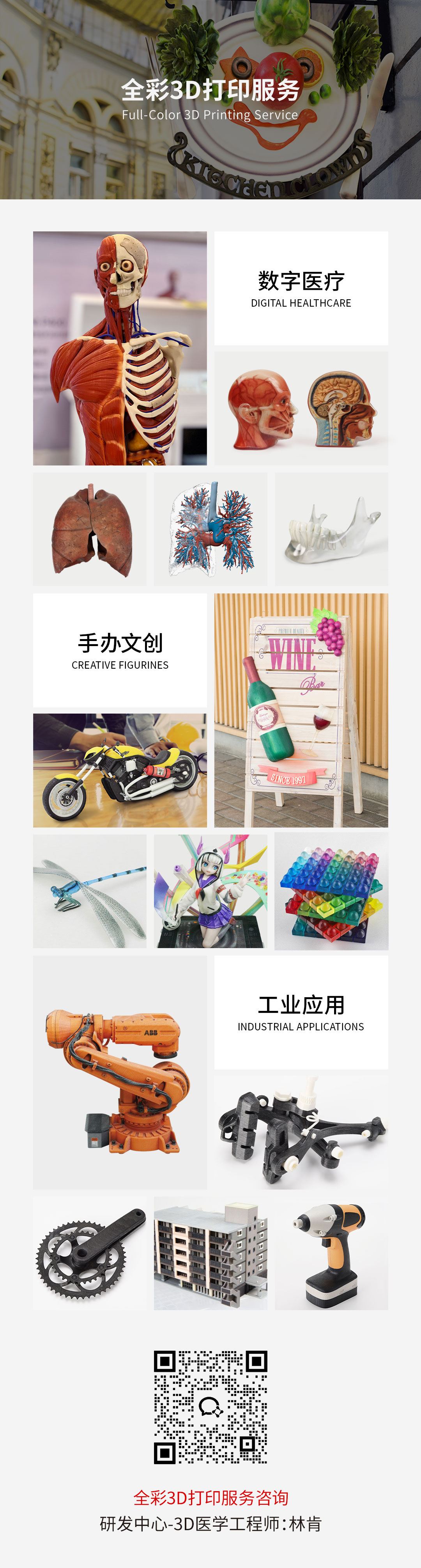
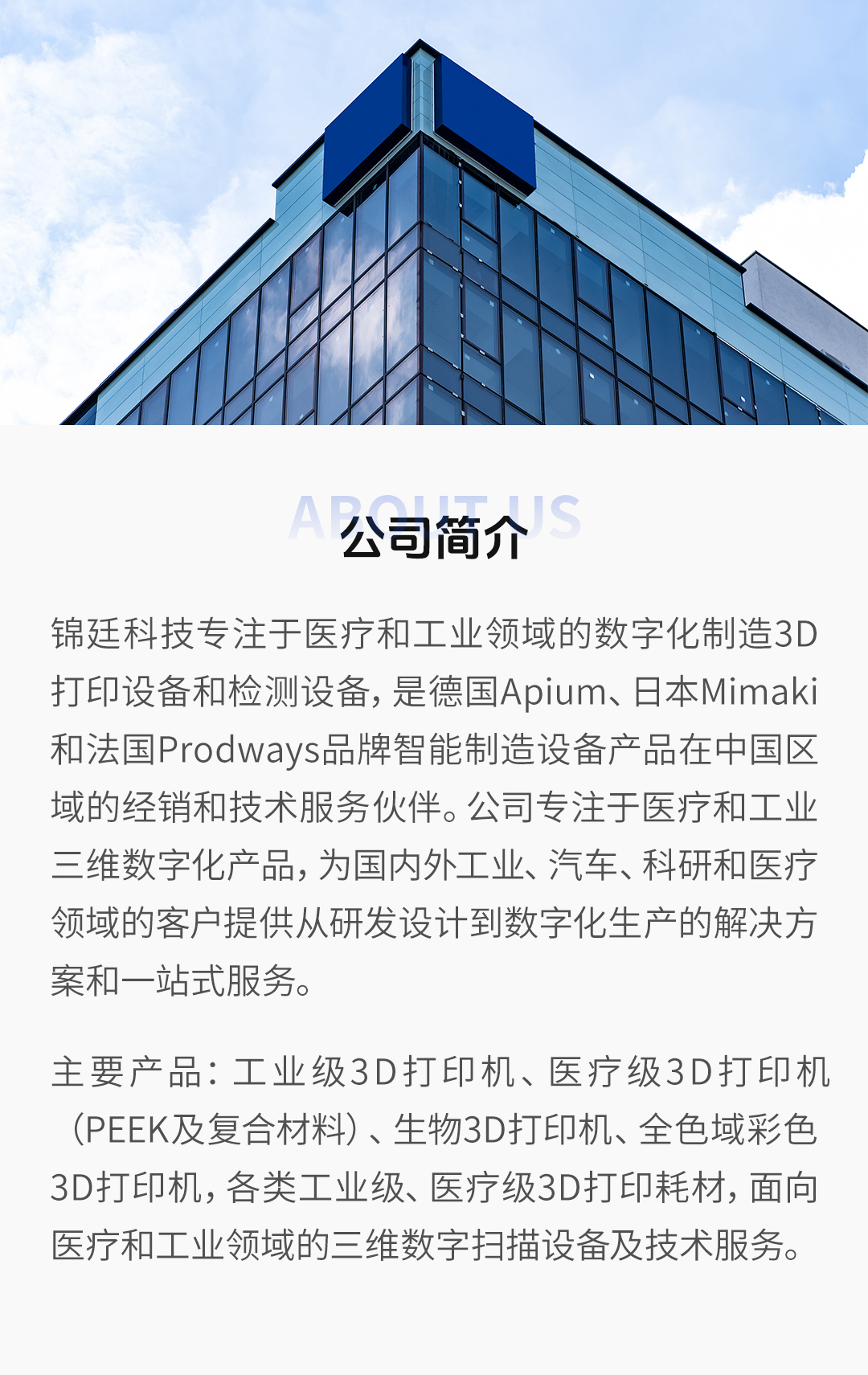
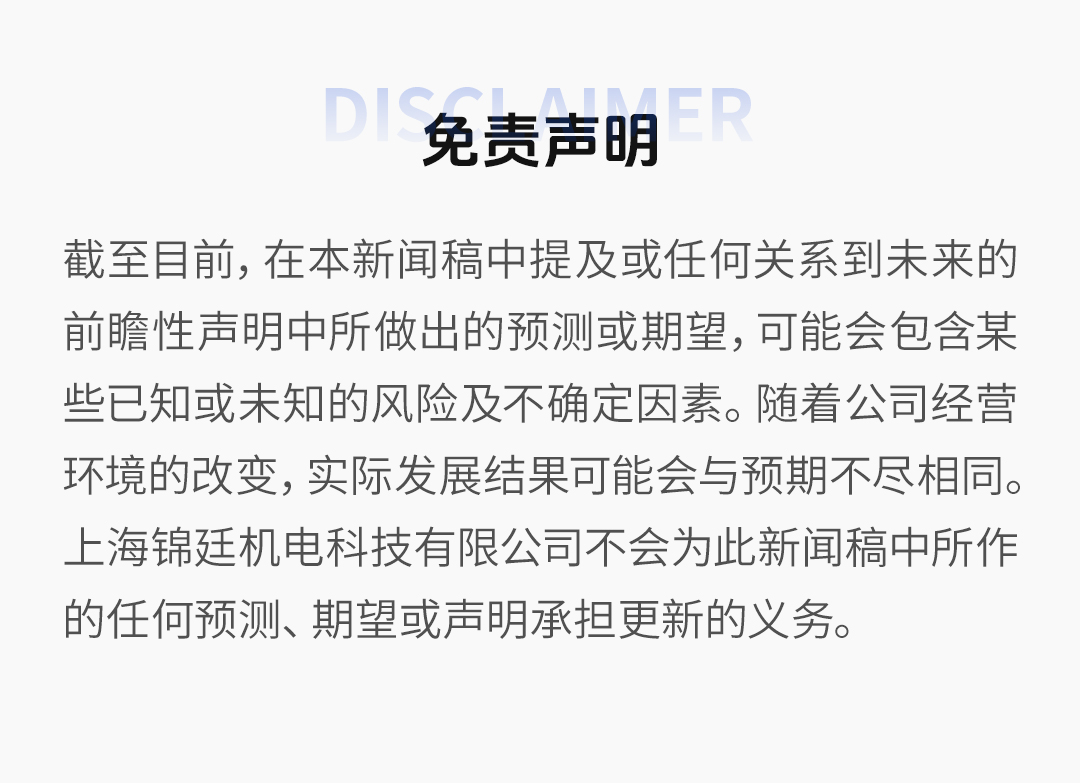